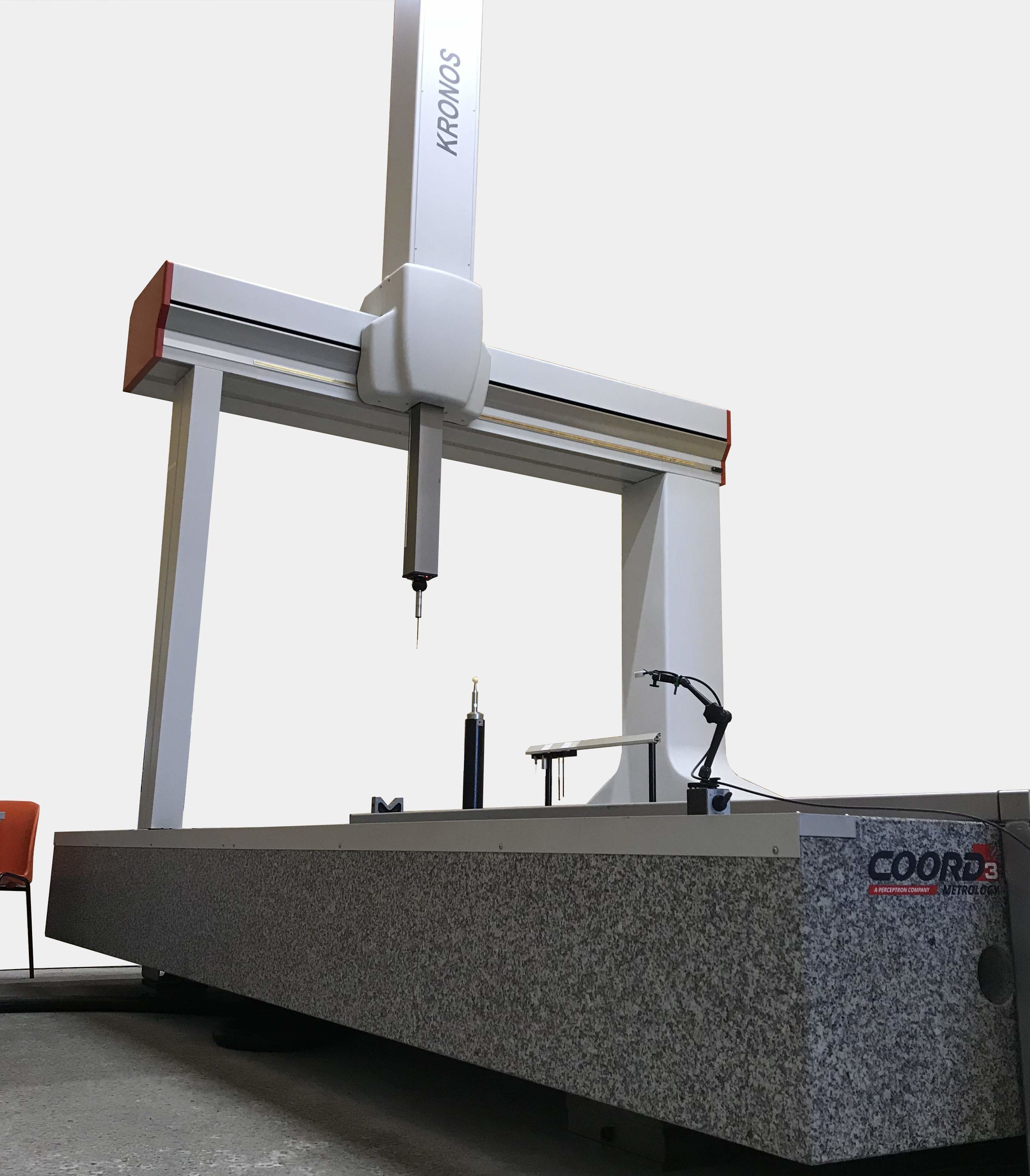
Il y a quelques mois, la société Galy Frères, spécialisée dans l’usinage de précision, a fait appel au savoir-faire de MCE Metrology pour améliorer ses performances en mesure de pièce. Un choix payant pour l’entreprise, basée en Ariège, et qui travaille avec de grands noms de l’aéronautique. Michel Tartié, Directeur Général, et David Estèbe, Directeur Technique, nous expliquent pourquoi.
Décrivez-nous votre société et son activité…
Michel Tartié : « Le groupe est constitué de trois filiales. Les deux premières font de l’usinage de pièces pour moteurs d’avions. Avec des matières dures, comme le nickel, le titane, et maintenant du René 65, un alliage nouveau. Nous créons et réparons également des moules et matrices pour fabriquer des pièces. La troisième filiale, ZNCI Aéro, réalise du contrôle, en majorité ultrason en immersion.
Nos sociétés sont certifiées ISO9001 et EN9100. Et nous avons également la certification de contrôle Nadcap (assurance qualité dans les secteurs de l’aérospatiale et la défense, NDLR).
Nous travaillons directement pour des groupes comme Aubert et Duval, Otto Fuchs, Praxair, Safran … et indirectement pour Rolls Royce, General Electric ou Ariane.
Le chiffre d’affaires cumulé atteint 7 millions d’euros. L’entreprise est en pleine croissance, nous sommes passés de 40 à 80 collaborateurs entre 2011 et aujourd’hui. »
Vous vous êtes équipés récemment d’une machine de mesure Coord3, modèle Kronos, auprès de MCE Metrology. Pour quelles raisons ?
David Estèbe : « Nous avions besoin de mettre en place une machine à mesurer tridimensionnelle automatique, pour contrôler des pièces de moteur essentiellement. Nous avons commencé à rechercher ce qui se faisait en 2017. »
Michel Tartié :« Nous avons déterminé notre besoin technique, notamment sur l’aspect dimensionnel. Choisi le logiciel, les critères de précision. Nous nous sommes rapprochés de trois fournisseurs, puis deux…
Au final, nous avons opté, auprès de MCE Metrology, pour une machine un peu plus grande que ce que nous envisagions au départ, pour quasiment le même prix… C’est cela qui a fait la différence. Et nous avons senti chez MCE Metrology une volonté forte de se faire référencer chez nos clients. »
David Estèbe : « Il nous fallait des dimensions suffisantes pour contrôler nos plus grosses pièces, des disques aux diamètres pouvant atteindre jusqu’à 1700mm de diamètre. Nous avons maintenant une capacité atteignant les 2 m de diamètre. Avant, nous contrôlions avec un bras de mesure. C’était moins précis, et cela nécessitait l’intervention constante d’un opérateur. Là, avec cet outil, tout est automatisé, l’opérateur est plus libre et peut réaliser d’autres opérations, contrôler d’autres pièces avec le bras, faire de la documentation. Et puis ces mesures sont plus sûres. C’est un gros gain en fiabilité. »
Comment s’est déroulé la mise en place de l’équipement avec MCE Metrology ?
David Estèbe : « Une personne de MCE Metrology a assisté en permanence à la mise en place et au démarrage de la machine. La formation s’est déroulée sur site. En complément, MCE Metrology a réalisé des programmes spécifiques pour le contrôle de pièces de grands volumes, nécessitant des configurations de stylets particulières.
Vous envisagez d’autres applications à cette technologie ?
David Estèbe : « En effet. On peut imaginer, à l’avenir, des contrôles par paquets, avec la fabrication de nouveaux outillages. Pour gagner encore en fiabilité et sur le coût des contrôles. »
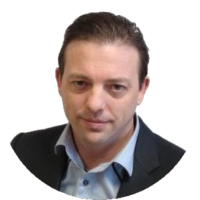
Merci à David Estèbe et Michel Tartié d’avoir accepté de répondre à nos questions
En savoir plus sur Galy Frères : www.galy-aero.fr